热模锻压力机的创新应用
文/于学宏,申刚,仉建军,朱元胜·青岛宏达锻压机械有限公司
随着国民经济的飞速发展和科学技术的日益提高,我国锻造业的社会化大生产也得到了快速发展,为了提高生产效益,锻造企业必将重新洗牌,逐步向集约化方向发展,走批量化发展之路,从而降低生产成本,提高效益。锻造设备也将进行升级改造,向优质高效、自动化、精密化方向发展,而热模锻压力机适合自动化、批量化生产的特点必将成为符合这一发展趋势的优选设备之一。
热模锻压力机性能特点
热模锻压力机(图1)是我国目前模锻行业广泛采用的模锻设备之一。它可以实现多模膛锻造,锻件尺寸精度较高,加工余量小,适用于大批量流水线生产中,其是模锻车间设备更新改造的优选设备之一。
在热模锻压力机上,可以完成开式模锻、闭式模锻和挤压等金属型材的各种热模锻工艺过程。通过手工操作或自动传送装置,可以进行多模腔的热模锻。
目前在热模锻压力机上模锻的零件主要类型有:
⑴主要通过镦粗方式成形的锻件,例如齿轮、法兰盘等盘形零件。
⑵主要用挤压成形复杂结构形状的锻件,例如叉形零件和其他非对称零件。
⑶需要用预先引伸工序的锻件,像汽车前梁、曲轴等。引伸工序通常在辊锻机上进行。
热模锻压力机使用选择
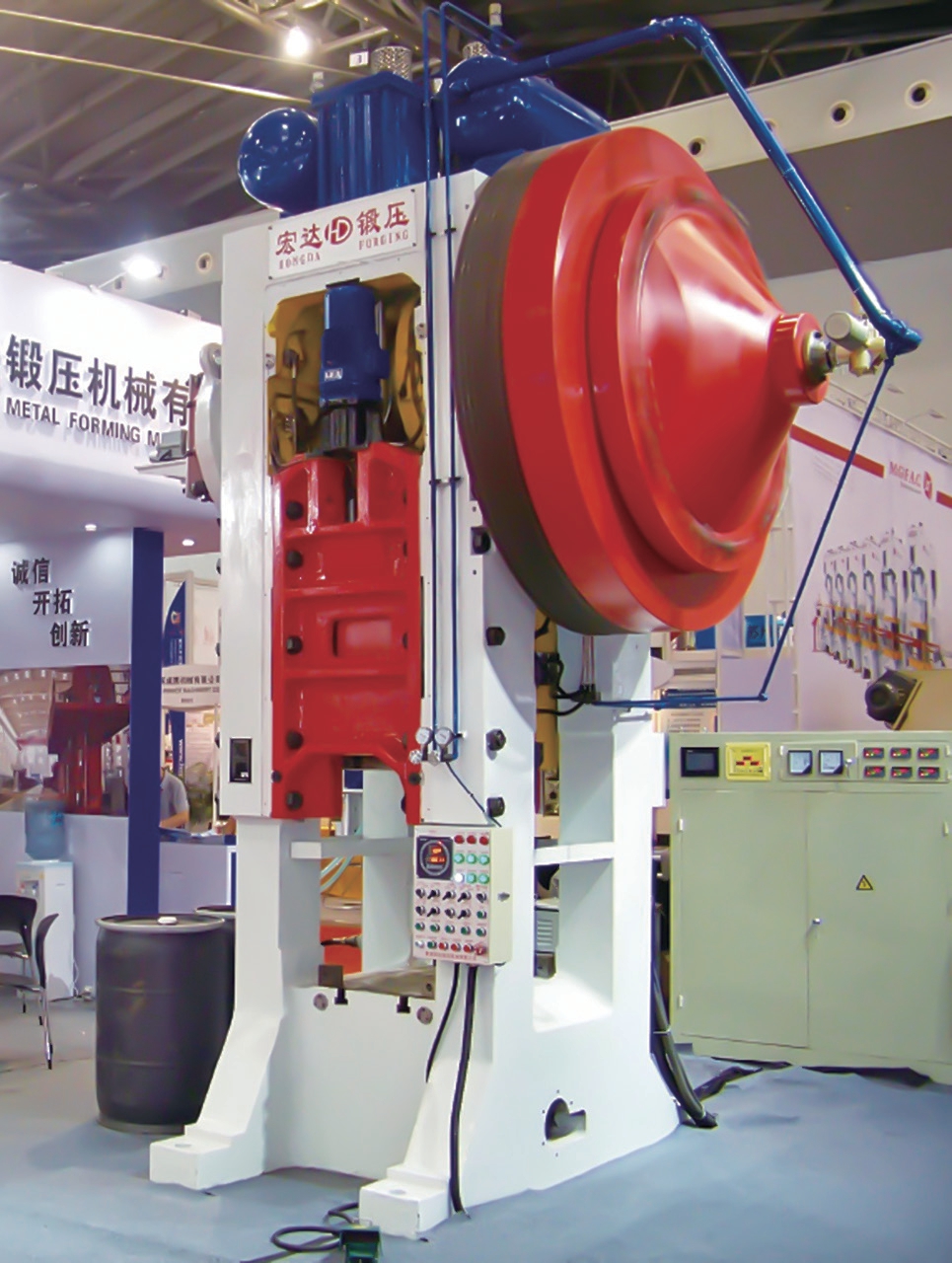
图1 MP-630 热模锻压力机
热模锻压力机的使用选择除考虑压力机的工作台上平面和滑块底面尺寸、行程、封闭高度及其调整量等参数外,最重要的是确定压力机的公称压力,与此同时还必须使模锻时所消耗的能量小于或等于压力机所能释放的最大能量。
在热模锻压力机使用过程中,毛坯加热温度过低、加热毛坯在锻造传送过程中的冷却、毛坯体积的公差以及压力机封闭高度的不正确调整等原因,都有可能引起模锻力的急剧增加,导致压力机过载或闷车,因此,正确选择热模锻压力机的公称力,仍然是保证热模锻压力机正常和可靠工作的一个重要手段。
选择热模锻压力机时,必须考虑到模锻力是锻造温度和毛坯体积的随机函数这一事实。
经验选择计算公式:pm=(0.7 ~0.75)Pg
式中:pm—锻造温度下的平均锻造力MN;Pg—热模锻压力机的公称压力MN;pm 可以根据工艺计算决定;系数0.7 适用于温度分散较大和非自动热模锻压力机;系数0.75 用于温度分散较小和自动热模锻压力机的情况。
我公司最新研制的MP 系列热模锻压力机,MP-1600 热模锻压力机(图2)结构及控制水平有以下特点:
⑴采用PLC 程序控制技术,可实现轴温监测、故障显示、曲轴转角数字显示、系统运行状态显示、自动润滑及润滑自动监控等,且具有工作量记录、轴温打印和慢速开车等功能。
⑵采用高强度整体或组合机身,整体实心铸造机身,立柱与上横梁、底座大圆弧过渡,抗疲劳性强、刚性好、精度高、外形美观。
⑶滑块采用“X”型对角线导轨,热敏度小,因此导轨间隙可以调的很小,导向精度高,锻件精度好。
⑷离合器、制动器采用浮动镶块式气动摩擦离合,发热轻、寿命长、结构简单,维护方便,且离合器具有过载保护功能。
⑸上下顶料采用内置液压缸顶料,上顶料避免了上死点打料造成的锻件摔坏、扭曲等问题。下顶料具有高度保持功能,高度保持时间可以设定,夹取锻件非常方便。
⑹封闭高度采用上调整、电机驱动,调整方便、灵活、可靠,避免了封闭高度下调整造成的氧化皮的侵入,也避免了下调整造成的模具水平移动而引起的错模现象。
⑺采用双点支撑式连杆,支撑面宽、抗偏载能力强。
⑻设有飞轮制动器、可使飞轮快速停止下来。
热模锻压力机的创新发明(一)
现有的热模锻压力机,滑块处在下死点位置时,离合器盘已脱开,飞轮只有储存的能量用于打击工件。因此,压力机在工作过程中,如出现锻件温度过低、模具调整不当、重复放入锻件、模具上留有硬性异物情况,都可能导致压力机过载出现闷车,损坏压力机,设备使用寿命短,危及人身安全。
本发明提供了一种防止压力机因过载而出现闷车的技术、使设备运行安全可靠、使用寿命长、该类压机是可保障操作人员人身安全的增压补偿式预防闷车的热模锻压力机。
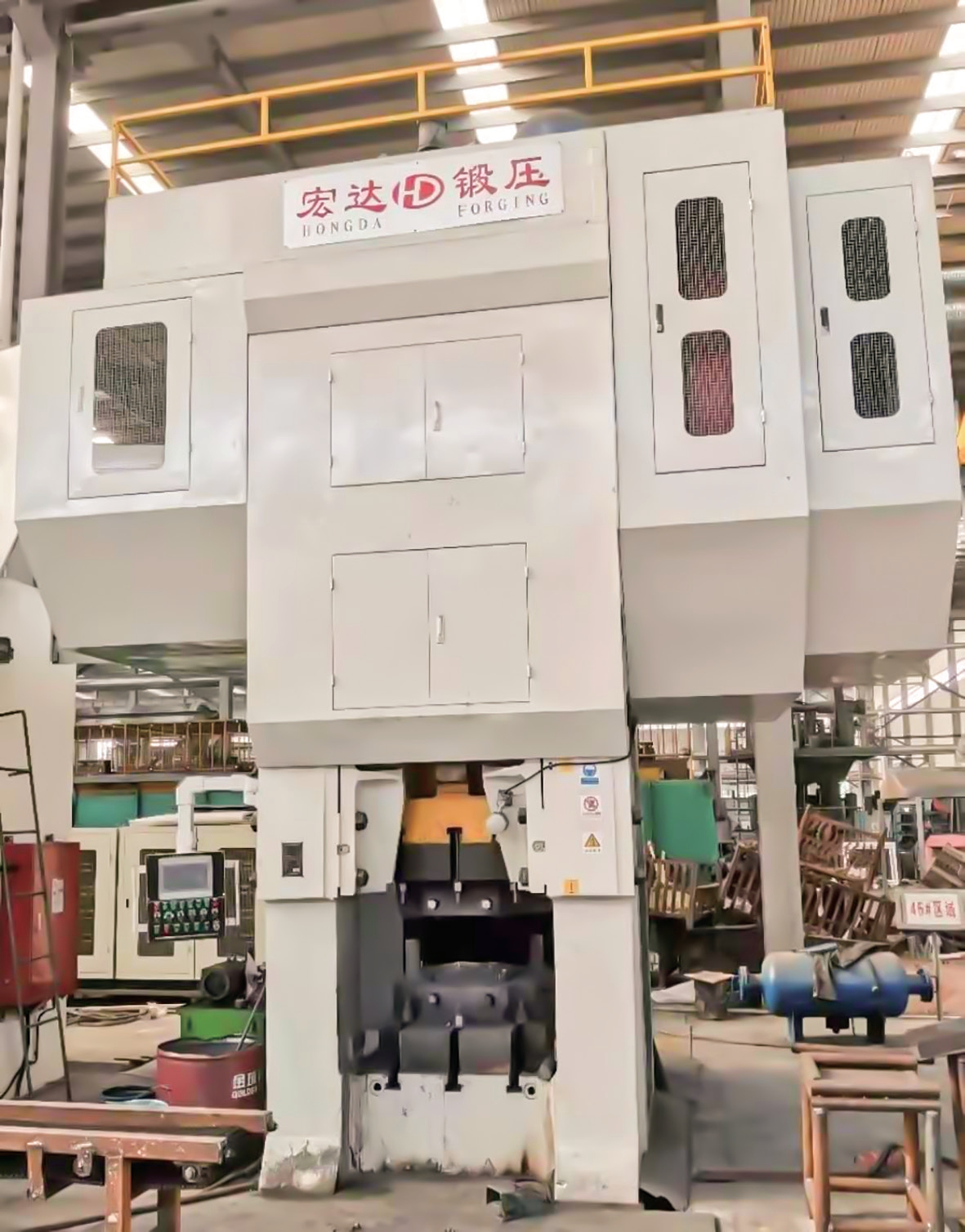
图2 MP-1600 热模锻压力机
其工作原理是:
⑴由电机上小皮带轮经三角皮带传动,带动飞轮转动,离合器活塞压靠离合器摩擦块,这样,离合器盘与飞轮一起转动,带动曲轴转动,曲轴的转动,带动滑块由曲轴上死点0°运动到曲轴下死点180°,然后返回上死点,就完成一个工作循环。在压力机正常工作情况下,离合器常断电磁阀一直处于断电关闭状态,气动增压补偿管道处于不通气状态。只有当接收到压力机将要闷车信号时,离合器常断电磁阀才通电,这时,气体通过气动增压补偿管道,进入离合器。
⑵当滑块处在上死点位置时,制动器电磁阀与离合器常通电磁阀断电,处在关闭状态,通向离合器、制动器的压缩空气关闭,飞轮空运转。在制动器弹簧压力下,制动器压环将制动器摩擦块通过中间制动器环形活塞,压紧在制动壳体的摩擦面上。制动器摩擦盘通过胀套与曲轴固定联接,使曲轴停止转动。同时离合器压缩空气关闭后,离合器活塞在离合器弹簧的作用下使离合器摩擦块脱开,固定在曲轴上的离合器盘与飞轮摩擦面脱开,因右钢套固定在机身上,右钢套外径上安装着左轴承和右轴承,这时飞轮空运转。
⑶当压力机滑块打击锻件时,制动器电磁阀与离合器常通电磁阀同时通电,压缩空气进入制动器和离合器工作腔。气体进入制动器后,制动器环形活塞推力大于制动弹簧力,制动器压环脱开制动摩擦块,制动器松开。同时,压缩空气经离合器旋转接头进入离合器气缸体内腔,推动离合器活塞压紧离合器摩擦块,运动经由键连接的离合器盘传给曲轴,曲轴作旋转运动,通过连杆带动与之连接的滑块向下运动。当滑块运动到下死点时,离合器常通电磁阀断电,压缩空气关闭,离合器活塞在离合器弹簧力的作用下脱开离合器摩擦块,此时,飞轮用储存的能量打击工件,锻件吸收能量后锻打成形。当曲轴旋转到270°时,制动器电磁阀断电,制动器压缩空气关闭,制动器制动弹簧开始制动,运行到上死点位置,滑块停止,完成一个工作循环。
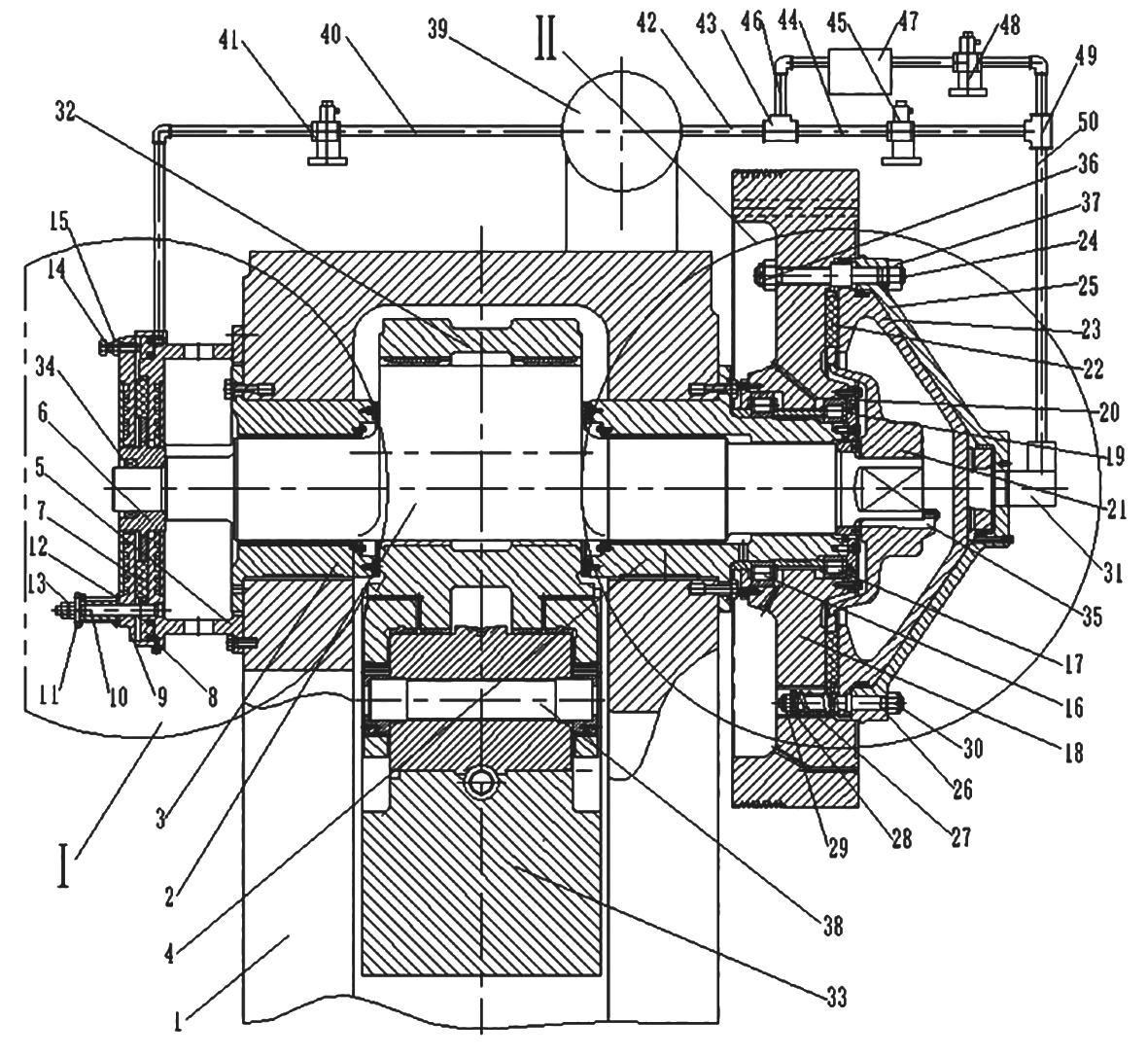
图3 气动增压补偿式热模锻压力机
气动增压补偿式热模锻压力机(图3),采用气动增压补偿系统,在设计中,首先根据设备刚度,确定一个过载参数。在压力机锻造过程中,出现过载时,控制系统采集到信号后,离合器常断电磁阀通电,这时,接通离合器增压阀的压缩空气,气动压力可增加1 倍,气动增压补偿管道通气,压缩空气通过离合器旋转接头进入离合器气缸体内腔,推动离合器活塞压紧离合器摩擦块,离合器盘带动曲轴作旋转运动,此时,飞轮重新结合,在获得大扭矩和动力驱动下,使滑块迅速脱离过载区,防止压力机因过载而出现闷车现象,运行安全可靠,设备使用寿命长,保障操作人员的人身安全。
热模锻压力机的创新发明(二)
现有的封闭高度调整系统,利用丝杠与丝母传动,指针进行直线运动,根据指针在标尺上的刻度读数,实现封闭高度调整。传统技术的传动结构复杂,读数靠机械标尺来标明,存在较大误差,精确度低,更实现不了数字化调整。
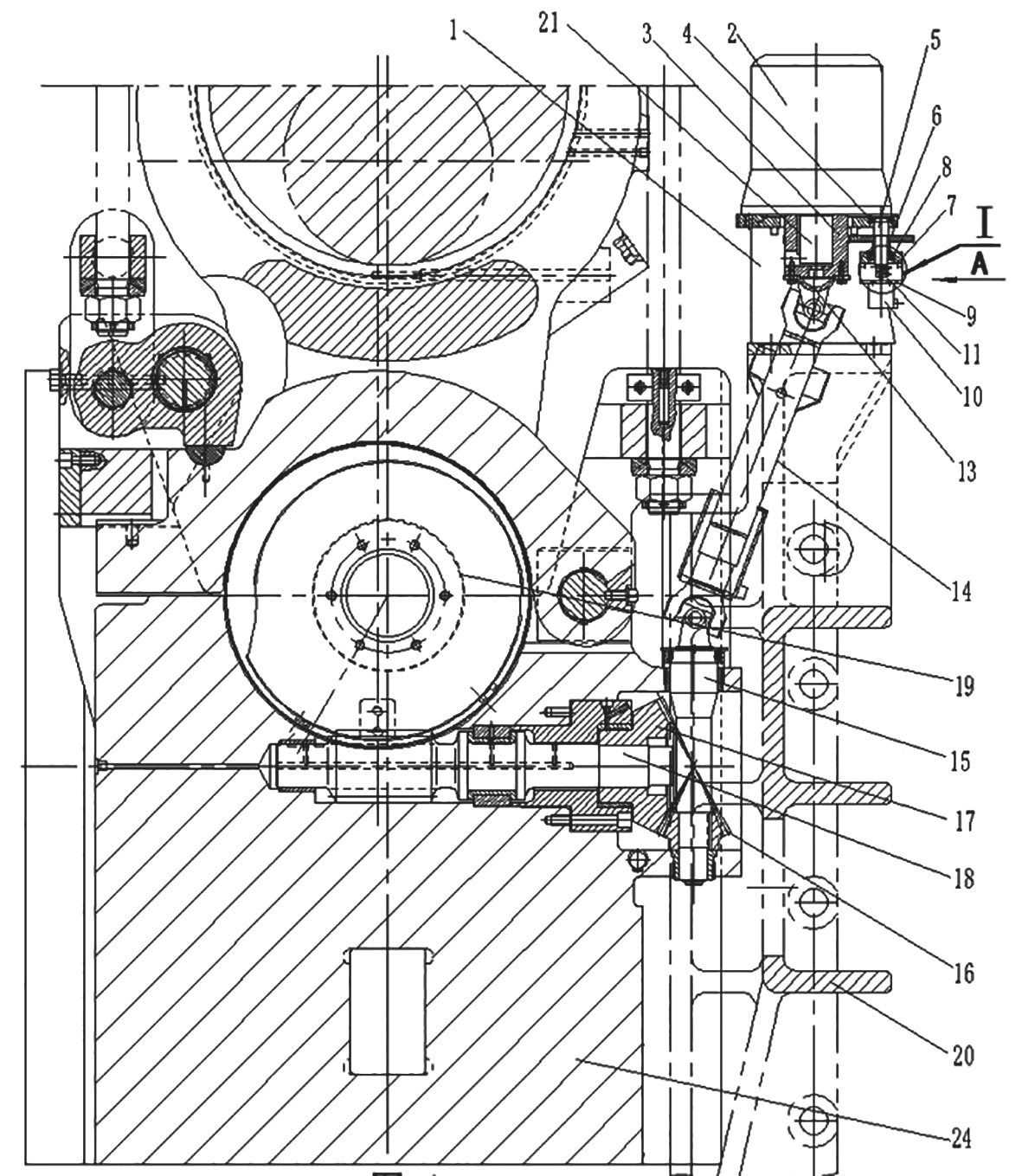
图4 模锻机微调智能调整及控制装置
本发明提供了一种精确度高、调整准确、确保编码器的稳定性与可靠性的模锻机微调智能调整及控制装置(图4)。其动力由立式电机提供给伸缩型万向联轴器,经立式传动轴、主动锥齿轮、从动锥齿轮、蜗杆传给偏心蜗轮,偏心蜗轮转动来改变滑块位置。同时,立式电机上的套式齿轮将运动传给从动齿轮,从动齿轮经键连接将旋转运动传给台阶式立轴,台阶式立轴再经联接套带动编码器旋转轴旋转,编码器采用绝对值编码器,它不需要连接计数器,通过光信号的位置来识别绝对角度位置,能够大大提高编码器的抗干扰及数据可靠性。传出信号直接由PLC 控制在按钮站触摸屏操作界面上对设备封闭高度进行调整,调整时可直接输入所需数据,实现智能微调及控制,精确度高,调整准确。
模锻机微调智能调整及控制装置,编码器通过连接架、支座、立式电机支架,最终固定在模锻机机身上,而不是安装在运动部件滑块上,避免了滑块快速移动打击工件时而产生的振动,确保了编码器的稳定性与可靠性。
模锻机微调智能调整及控制装置,利用编码器数字化技术,精确度高,进行数字补偿而实现封闭高度调整,调整准确。模锻机封闭高度直接数字显示,无需用肉眼在传统标尺上读数,误差极小,精确度高,直观性强。
结束语
经过实践证明,我公司采用以上发明创新的热模锻压力机,结构简单,安全可靠,使用方便,故障率低,能给企业带来很好的经济效益,也将为我国锻造企业的产业重组和转型升级提供适合批量生产的装备保障。
随着国民经济的飞速发展和科学技术的日益提高,我国锻造业的社会化大生产也得到了快速发展,为了提高生产效益,锻造企业必将重新洗牌,逐步向集约化方向发展,走批量化发展之路,从而降低生产成本,提高效益。锻造设备也将进行升级改造,向优质高效、自动化、精密化方向发展,而热模锻压力机适合自动化、批量化生产的特点必将成为符合这一发展趋势的优选设备之一。