变形量对余热淬火链轨节锻件晶粒度的影响
文/英成业,周琦,吴岳岭·山推工程机械股份有限公司
锻造余热淬火是在锻造后利用锻件自有的余热直接进行热处理,它将锻造与热处理两工序紧密结合在一起,实现了两工序的合并,节省了工件后续热处理的再次加热,是一种大量节约能源的有效途径,目前已在汽车、工程机械行业得到广泛应用。
采用余热淬火工艺生产的产品,具有优秀的综合力学性能,但与采用常规调质热处理生产的产品相比,其晶粒度较低,采用余热淬火工艺生产的产品,其晶粒度通常要比采用调质工艺生产的产品低1 ~2 级。影响余热淬火锻件晶粒度的因素见表1。
由于受到各种因素的制约,锻件在进行批量生产时,其产品形状、使用的原材料、采用的设备一般是无法改变的。此时,若要提高余热淬火锻件的晶粒度,需要对锻造工艺进行调整。影响锻件晶粒度的工艺因素主要有三点,包括锻造温度、锻造后至淬火前的时间、各锻造工步间的变形量。通过降低锻造温度,减少锻造后至淬火前的停留时间,能够控制晶粒长大,提高锻件晶粒度。
实际生产中,考虑到锻件的质量和产线的布置,工艺参数调整的区间范围是有限的。以我公司某链轨节锻件产品为例,锻造加热温度为(1180±30)℃,锻后入油时间为35s 以内,经验证,在此范围内对锻造温度及锻后入油时间进行调整,对锻件晶粒度无明显影响。
表1 影响余热淬火锻件晶粒度的因素

锻造过程是通过高温下塑性变形引起的动态再结晶,达到细化晶粒的效果。根据临界变形区理论(图1),当变形量大于临界变形时,金属内部均产生了塑性变形,因而再结晶时,同时形成很多核心,这些核心稍一长大即互相接触了,所以再结晶后获得了细晶粒。但是在实际生产中,尤其对于形状复杂的多工位模锻件,由于其变形工步多,各工步间变形过程复杂,因此很难直接判断其各工位间锻件晶粒度的变化规律。本文以我公司某链轨节锻件产品为例,通过试验对多工位模锻过程中各工步锻造变形量对余热淬火锻件晶粒度的影响进行了研究。
各工位模锻件晶粒度变化规律
该链轨节锻件锻造工艺为:棒料→压扁→预锻→终锻→冲孔切边,为研究各工位锻件晶粒度的变化规律,分别取每个工位的锻件,在950℃下进行油淬,并在锻件相同位置取样剖切以观察其晶粒度。试验件如图2 所示,试验结果见表2。
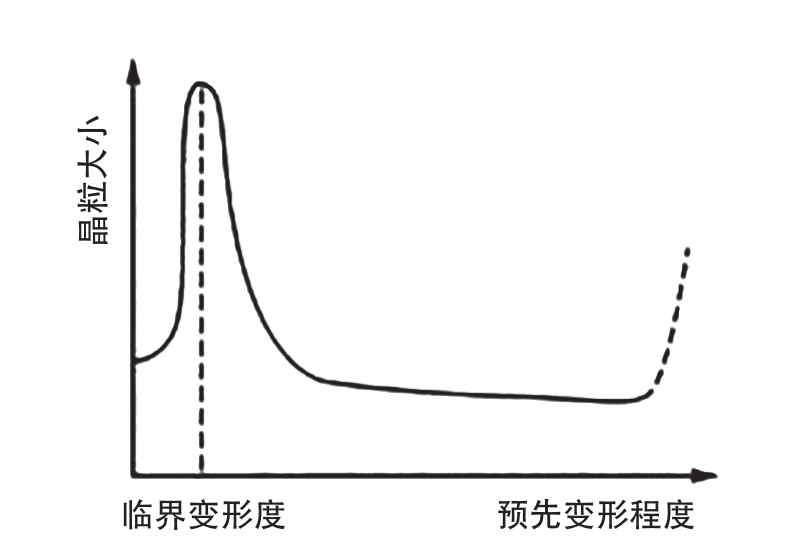
图1 变形程度与晶粒度的关系
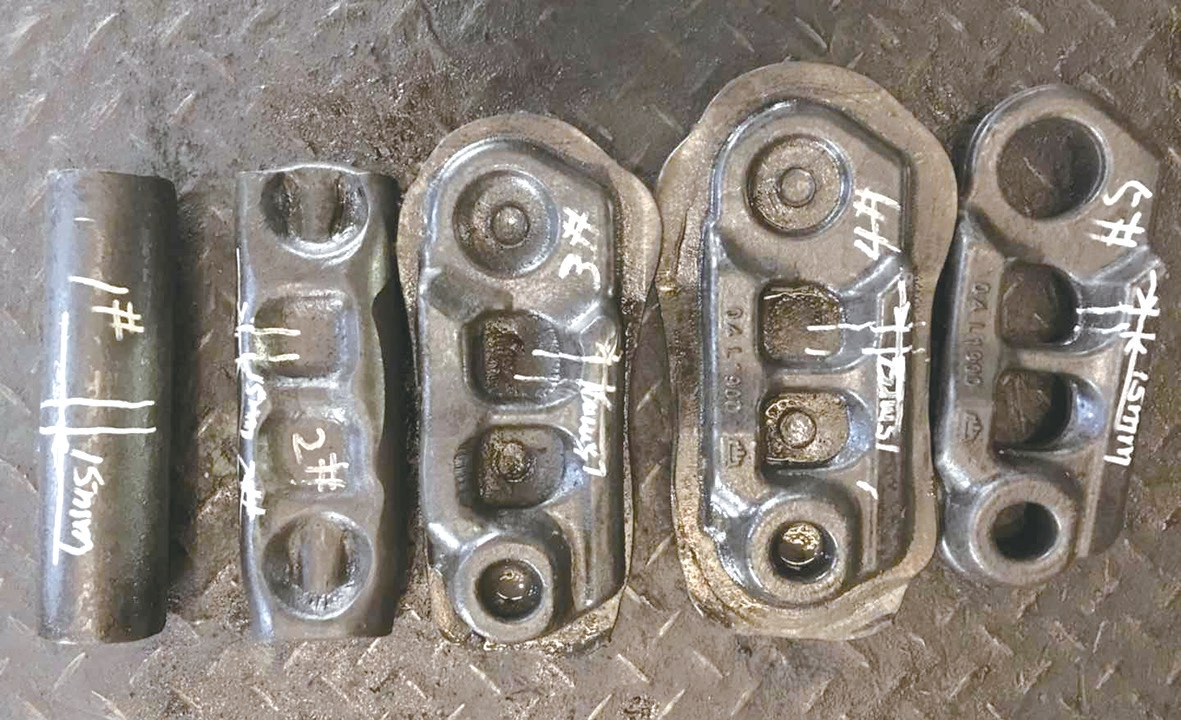
图2 不同工位的淬火锻件
可以看到,由棒料直接成形得到的终锻件,其晶粒度级别最高为4.8 级;增加了预锻工位之后,从棒料到预锻件,晶粒度由3.0 级提高至4.5 级,从预锻到终锻晶粒度基本无变化;继续增加压扁工位,从棒料到压扁件,晶粒度提高了0.7 级,从压扁件到预锻件,晶粒度提高了0.4 级,从预锻到终锻晶粒度无变化,此种工艺得到的终锻件晶粒度最低仅为4.1 级。
由此推断,链轨节锻造过程中晶粒的细化主要是在棒料到预锻的变形过程中完成的,预锻以后的终锻以及冲孔切边工位,对晶粒度基本无影响。并且随着变形工步的增多,由于各工步间变形程度减小,锻件晶粒度变差。
变形量对晶粒度的影响
工件在压扁工位上变形时,坯料的高度减小,横截面积增大,基本上属于镦粗成形。而工件在预锻工位上的变形复杂,坯料局部是以镦粗压入的方式成形,高度减小;局部是以挤压的方式成形,高度增加。锻件晶粒的细化是在这两步成形过程中完成的,对于锻件局部来说,其过程复杂,需要通过试验进行验证。根据以上情况,设计试验,分别改变压扁工位和预锻工位的变形量,记录不同变形量下终锻件晶粒度的变化趋势。
表2 不同锻造工艺下各工位锻件晶粒度

由图3 可以看到,随压扁工位件厚度增加,终锻件晶粒度降低;随预锻工位件厚度增加,终锻件晶粒度提高,如图4 所示。
结束语
根据以上规律,我公司对该产品压扁及预锻工位模具进行了重新设计,锻件心部晶粒度全部达到客户要求等级以上,且平均值由4.1 级提高至5.2 级。

图3 晶粒度与压扁工位件厚度的关系
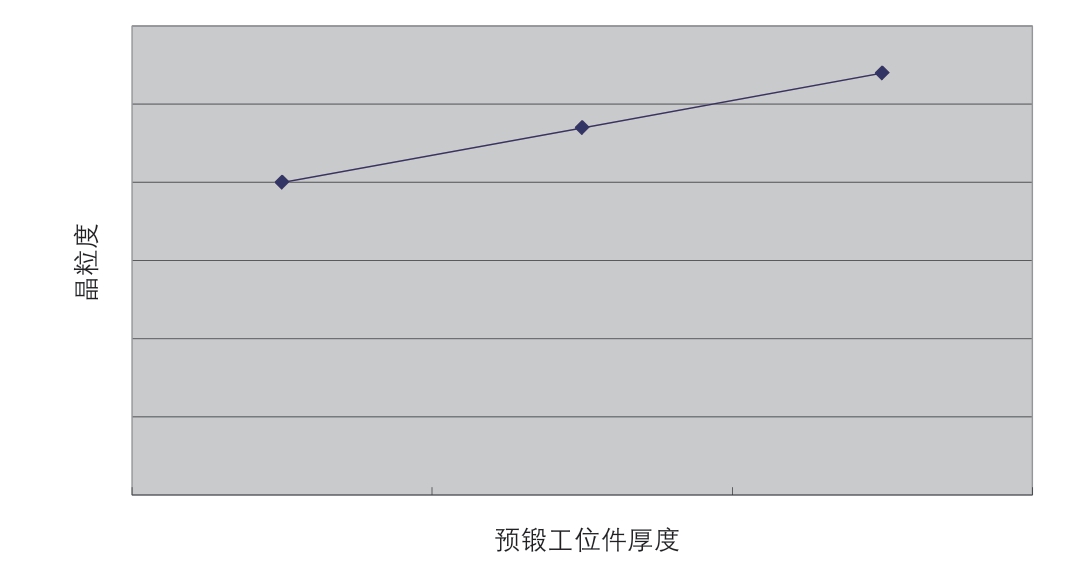
图4 晶粒度与预锻工位件厚度的关系
对于此链轨节锻件,减小其压扁工位件厚度,增加其预锻工位件厚度,能够增加锻造成形过程中各工位间的变形程度,提高其晶粒度。同样,对于其他模锻件来说,各工位间的变形越剧烈,锻造过程中的晶粒细化效果越好,最终得到的锻件晶粒度越高。在实际生产中,各工位间变形量的设计受到锻件质量、模具寿命、设备能力等多方面因素的制约,因此不能随意增加,但是可通过设计人员的经验、现场试验、软件模拟等多种方法寻找其最优值。
锻造余热淬火是在锻造后利用锻件自有的余热直接进行热处理,它将锻造与热处理两工序紧密结合在一起,实现了两工序的合并,节省了工件后续热处理的再次加热,是一种大量节约能源的有效途径,目前已在汽车、工程机械行业得到广泛应用。